L’impression 3D : un métier
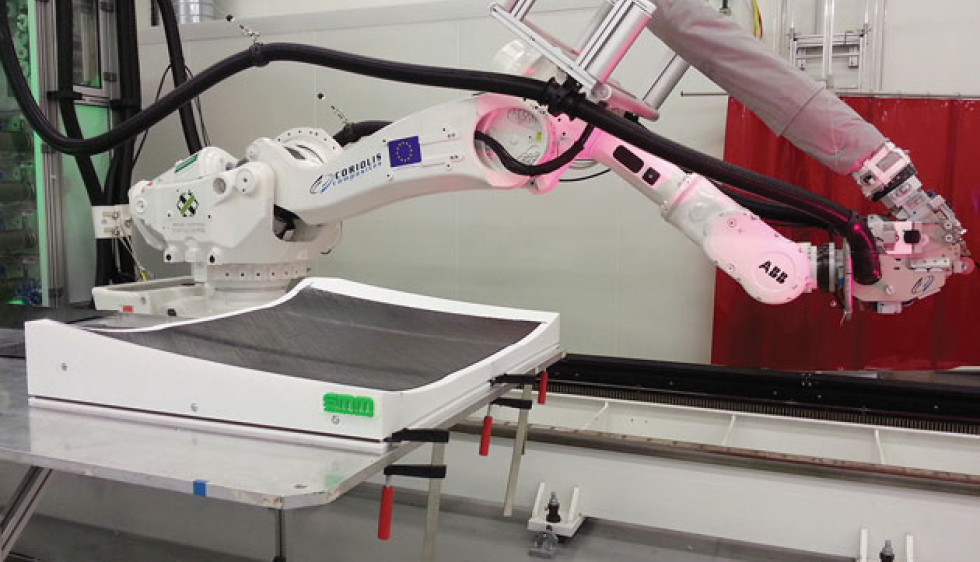
La société de Franck Doyen est spécialisée dans la fabrication additive en plastiques composites pour l’industrie.
Sciences Ouest : Pouvez-vous nous présenter votre métier et vos machines ?
Franck Doyen : J’ai créé Addium en 2014 et nous sommes spécialisés dans la fabrication additive - impression 3D - de pièces en plastique composite, façonnées à la demande pour des clients industriels. Nous possédons trois machines, de la plus petite à la plus grosse. Les plus petites peuvent imprimer des objets de 25 à 30 cm(1) tels que des boîtiers, des supports de piles... pour des clients dans le domaine de l’électronique, par exemple. Ou bien alors des prototypes.
Avec la plus grosse(2), nous approvisionnons le marché de l’outillage pour les secteurs de l’automobile et de l’aéronautique. Nous fabriquons des outils de perçage, de fraisage, des moules... qui sont des pièces quasi uniques.
SO : Comment ces pièces étaient-elles fabriquées avant ?
FD : Les pièces d’outillage étaient en aluminium et fabriquées par usinage. Mais l’aluminium est plus cher, plus lourd que les thermoplastiques utilisés en fabrication additive. Et pour une même durabilité des pièces, l’usinage est un procédé plus long.
SO : On peut parler de révolution, non ?
FD : Oui, cela change pas mal de choses, notamment dès le début du processus de création, au moment où l’on commence à imaginer la pièce. Mais il faut encore que cela entre dans le chemin de pensée des concepteurs et des bureaux d’études. Cela commence, notamment chez les jeunes diplômés qui ont eu l’occasion de découvrir la technologie pendant leurs études. Le premier brevet sur la fabrication additive a pourtant été déposé en 1984 ! Pour la fabrication de pièces prototypes dans l’industrie. Mais elle y est restée confinée. Car c’était de la résine qui était utilisée au début. Cela donnait un très bel aspect de surface, bien lisse, mais les objets étaient très fragiles et les dimensions pas toujours respectées de façon précise...
SO : Pourquoi l’impression 3D explose-t-elle maintenant ?
FD : Grâce à l’évolution simultanée des matières premières et des machines. On arrive maintenant à renforcer les thermoplastiques de base comme l’ABS(3) en les enrichissant avec du carbone pour améliorer leurs propriétés mécaniques ou avec du Kevlar pour obtenir une meilleure résistance aux chocs. Nous travaillons d’ailleurs beaucoup avec la société Nanovia(4) qui fabrique même la “Rolls du plastique” ! Le PEI pour polyétherimide, qui peut résister sans fléchir à une température de 200 °C, contre 100 °C pour les ABS.
Et puis la révolution vient aussi des imprimantes. Outre le fait que certaines sont maintenant accessibles aux particuliers, les machines professionnelles comme celles que nous utilisons concurrencent l’usinage en termes de précision. On arrive à imprimer au dixième de millimètre près !
SO : Comment avez-vous rencontré ComposiTic ?
FD : En rentrant chez mes parents, dans mon Finistère natal ! Addium est implanté à Nantes et un jour un client m’a parlé du plateau ComposiTic à Lorient. Je m’y suis arrêté, et on s’est tout de suite compris ! C’est comme cela que j’ai découvert Nanovia. Nous formons le trio de la 3D bretonne ! Je bénéficie de l’expertise matériaux de Nanovia, de l’expertise impression 3D de ComposiTic et j’apporte le côté applicatif : je vois tout de suite l’intérêt, ou non d’imprimer en 3D.
SO : Comment voyez-vous l’avenir ? Quels sont vos prochains challenges ?
FD : Aujourd’hui, même avec de grosses imprimantes, on est limité par le côté fermé de la machine. On pourrait lever ce verrou en travaillant sur le développement d’un robot de type bras pour pouvoir réaliser des pièces de très grande taille.
(1)Les dimensions des petites imprimantes en longueur, largeur et hauteur sont : 250 mm, 250 mm, 305 mm. (2)Dimensions : 900 mm, 600 mm, 900 mm. (3)Pour acrylonitrile butadiène styrène. (4)Lire p. 10 à 12.
Franck Doyen
tél. 06 32 38 87 50
franck.doyen@addium.fr
TOUT LE DOSSIER
du magazine Sciences Ouest